目录
1. 提高机器的效率
2. 在现有PLC系统中添加高级I/O和高级信号处理功能
3. 将PAC集成至现有PLC系统
4. 总结
提高机器的效率
集成工业系统(I2S),一家数十年来专门生产现有金属轧机设备与控制系统的私营美国OEM公司,为我们提供了一个关于如何改善现有PLC系统的极佳范例。多年来,I2S一直使用PLC实现其所产轧机的自动化和控制。近年来,该公司业已开始尝试升级其轧机控制系统以改善效率与质量。为了升级该系统并改进其机器设备,I2S需要这样一个解决方案,它能提供更高的模拟输入精度以便实现与其伽马测量传感器的接口,以及高级信号处理功能,以提取来自传感器的模拟信号并将该信号转换为一个极为准确的厚度测量值(PLC将在轧机控制循环中使用这一测量值)。
为了节约时间与成本,I2S首先尝试在现有PLC系统中实现高级模拟测量与处理功能。当发现PLC无法提供所需的精确模拟I/O与信号处理功能时,I2S转向了NI CompactRIO——一个可重新配置的嵌入式PAC系统。
在现有PLC系统中添加高级I/O和高级信号处理功能
NI CompactRIO拥有一个嵌入式FPGA芯片与一个实时处理器,您可以通过内置的NI LabVIEW功能模块对其进行编程控制。CompactRIO还具有超过30个模拟与数字I/O模块,这些模块包含内置的信号调理(包括抗混叠、隔离、ADC和DAC等)、高速定时(模拟I/O高达800 kHz,数字I/O高达30 MHz)和高精度(高达24-位ADC)处理模块,以便与任一工业传感器或执行装置相连接。

I2S将CompactRIO模拟输入模块连接至伽马厚度传感器,以提供执行必要精度测量所需的高速定时与精度。由于每个I/O模块直接与FPGA相连,I2S工程师们可以利用LabVIEW FPGA方便地定制CompactRIO模拟I/O速率。
从伽玛传感器采集模拟数据之后,CompactRIO实时处理器利用内置的LabVIEW实时浮点功能模块,将来自传感器的数据转化为一个准确的厚度测量值。CompactRIO运行FPGA与实时处理器中的I/O与信号处理的所有功能,并将一个极为准确的厚度测量值发送至所连接的PLC,丝毫没有降低现有PLC控制循环的速率。
将PAC集成至现有PLC系统
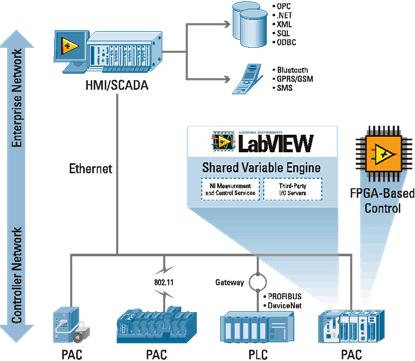
将PAC连接至现有PLC架构的三种基本方法:
1. 基本模拟与数字I/O——可以将模拟和数字数据从PAC输出至PLC。这也是I2S将处理后的数据从CompactRIO PAC输出到运行轧机控制循环的PLC所采用的方法,
2. 工业网络——大量的PAC产品支持工业协议,如DeviceNet、Profibus和CANopen,以及基于以太网的协议(如TCP/IP、UDP和Modbus TCP/IP)。I2S选用以太网协议实现CompactRIO PAC间的数据传输,以及PAC、PLC与联网HMI间的接口。
3. OPC连接——PAC也可以充当过程控制(OPC)客户或服务器的OLE,与PLC或其它使用OPC标记的PAC收发网络数据。OPC标准提供了一组通用的例程,该例程给出了方便实现来自不同厂商的自动化系统的接口。
在I2S,每台轧机包含三个联网的CompactRIO系统。其中,连接至基于伽马的传感器的两个CompactRIO系统,执行模拟输入测量和高级信号处理功能,以计算精确的厚度测量值。第三个CompactRIO系统接受来自其它两个系统的厚度测量值,并将一个模拟测量值输出至控制轧机的PLC。
处理后的数据通过以太网,以小于20毫秒的间隔在联网的CompactRIO系统间传送。CompactRIO测量值的采集、处理和传送,均以足够快的速度将精确的厚度测量值输入至PLC控制循环,而不会降低控制循环的速度。利用带有10/100 Mbps以太网端口的基于LAN的CompactRIO系统,I2S可以通过一个标准的TCP/IP协议,方便地连接至联网的Allen-Bradley PLC和HMI系统。
总结
在未来的数年中,工程师与科学家们将继续使用PLC实现我们所处环境的自动化,但随着机械装置的进步和自动化效率的提高,PLC往往无法单独完成所有任务。PAC技术为PLC提供了很好的互补,它增加了传统PLC无法提供的高性能I/O和处理能力。通过多种可用于连接PAC与现有PLC架构的方法,工程师们现在拥有了一种提高其基于PLC的自动化系统的简便方法。