应用领域:液压系统控制、信号采集、试验状态监测、数据处理
挑战:连杆是发动机的关键部件之一,其可靠性对整机寿命具有至关重要的作用。为了研究发动机连杆在拉压载荷下的疲劳特性,所研制的发动机连杆试验台基于美国NI公司的LabVIEW开发环境和CompactRIO嵌入式控制器,采用液压伺服的加载方式对连杆进行拉压加载。如何根据发动机及连杆的参数确定加载载荷和加载频率?如何控制液压系统按照设定的加载载荷和频率进行加载?如何实时监测试验状态,判断连杆发生疲劳破坏?如何采集、存储、分析相关数据得出相应的试验结果?这是整套试验系统的关键所在。
应用方案:CompactRIO 包含一个实时控制器与可重配置的现场可编程门阵列(FPGA)芯片,并且包含8个热插拔工业I/O插槽,具有非常好的可靠性和实时性; NI提供了针对各种类型信号的输入输出板卡与CompactRIO 相匹配,组成完善的硬件系统;NI LabVIEW包含强大的控制、采集、监控、分析等方面的函数,为整个试验系统提供完备的软件设计平台。
使用的产品:
LabVIEW 2009
LabVIEW RT 9.0
LabVIEW FPGA 9.0
LabVIEW PID Control Toolkit 9.0.0
CompactRIO-9014可重新配置嵌入式机箱
CompactRIO-9014嵌入式控制器
CompactRIO-9237应变信号采集模块
CompactRIO-9205电压信号采集模块
CompactRIO-9263电压信号输出模块
CompactRIO-9401 DIO模块
CompactRIO-9485 SSR模块
正文:
一. 引言
强度、刚度和疲劳寿命是衡量工程机械机构和零件可靠性的主要参数,疲劳破坏是机械机构和零件失效的主要原因之一(据统计,连杆60%到90%的破坏都是疲劳破坏),而引起疲劳破坏的主要原因是动态交变载荷。
连杆是往复活塞式内燃机的核心部件,也是内燃机中承受较大交变载荷的主要部件之一,其可靠性直接影响内燃机运行的安全。
目前开展连杆疲劳可靠性研究的主要手段包括仿真计算、实机试验和模拟疲劳试验。
仿真计算方便、快捷、成本低,针对连杆的仿真计算很多,但只能对疲劳可靠性进行趋势性的分析和验证,并且边界条件不确定;实机试验可以反映连杆的真实工况,但试验周期长、成本较高,并且不能进行强化试验;模拟疲劳试验可以用较短的周期较高的效率来进行试验,并可以对疲劳试验进行强化,更全面的检验连杆的疲劳特性。
目前,国内多为国外引进设备,尚未有自主研发的连杆拉压模拟疲劳试验台。因此,研制发动机连杆拉压模拟疲劳试验台具有较大的意义。在试验台的开发上,美国NI公司的LabVIEW开发环境和CompactRIO嵌入式控制器及其配套板卡为我们提供强有力的工具。
二. 试验系统总体介绍
2.1连杆受力情况
如图1所示,在发动机运行过程中,连杆的运动状态比较复杂,小头作往复运动,大头作旋转运动,杆身作平面运动。同时,连杆的受力情况也十分复杂,连杆在实际工况中的受力可分为两部分:一部分是工作中产生的气体爆发压力和活塞组件的往复惯性力;另一部分是连杆运动时本身产生的惯性力,包括往复惯性力,摆动离心力和横向弯矩(横向弯矩相对较小,并且其极值不与其他力一同出现,因此忽略不计)。
在以上各力的作用下每一个截面上都会有弯矩、剪力和法向力。但弯矩和剪力与法向力相比都不大,连杆主要承受的是交变的拉压载荷。
2.2试验原理
试验台的设计主要考虑连杆在实际运行中的拉伸压缩载荷,忽略弯矩与剪力,对连杆进行拉压加载。这种设计虽然不能完全模拟连杆得实际工况,但基本上可以比较准确的反映连杆的拉压疲劳特性,达到台架模拟试验的目的。
本试验台架可对连杆试件进行静载试验和动态疲劳试验。静载试验时,只对连杆试件缓慢施加拉力或者压力以考察连杆静态材料特性;动态疲劳试验时,对连杆试件施加交变拉压载荷,由于在发动机实际运行工况下连杆承受的最大压缩载荷要大于最大拉伸载荷,试验台采用非对称的加载方式,即负荷比不为-1。完成试验后,试验系统都会保存所有试验数据,包括应变信号、拉压载荷信号、循环次数、疲劳破坏状态等。通过对试验数据的统计分析,实现对连杆疲劳寿命的评估及其可靠性设计。
整个试验系统的控制通过美国NI公司的LabVIEW开发环境和CompactRIO嵌入式控制器来实现,主要包括液压加载控制,数据采集、存储、分析,试验系统的监控和安全控制等工作。
一. 试验系统总体方案设计
整个试验系统的设计可分为硬件和软件两个部分。
3.1 硬件设计
本试验台的硬件主要包括机械台体、液压加载系统和控制系统。
3.1.1机械台体
如图2所示机械台体采用四立柱的结构,主要功能是固定连杆试件,支撑其他机构进行试验。主要包括连杆试件固定夹具、移动导轨、移动面、支撑面。
3.1.2液压加载系统
液压加载系统主要功能是为模拟疲劳试验提供预先设定的加载载荷。其结构如图3所示,主要包括液压伺服电磁阀、液压放大器、液压油缸、液压泵站和蓄压器,同时还包括滤油器、单向阀、溢流阀等辅助液压器件。
液压伺服电磁阀采用德国Rexroth公司的三位四通阀,其中P为高压油路、T为回油油路、A与B为工作油路;液压放大器用于对液压压力的放大,以提供更大的加载载荷;液压油缸为单杆双作用活塞液压缸,用于执行对连杆试件的加载;蓄压器用于保持试验系统压力稳定,两个蓄压器分别位于回油油路和高压油路;滤油器用于过滤液压油;单向阀用于防止压力油回流到液压泵站;溢流阀用于防止压力过高,使系统压力保持在规定值以下。
液压伺服阀通过改变P、T与A、B的通断状态使液压缸上下运动进而实现对连杆的拉伸加载和压缩加载。
3.1.3控制系统
控制系统是与LabVIEW开发环境相结合的NI硬件,主要包括嵌入式控制器CompactRIO 9014,NI 9237AD模块,NI 9205AD模块,NI 9263DA模块,NI 9401DI/O模块,NI 9485SSR模块。
如图4所示NI CompactRIO嵌入式测控系统与PC机组成整个试验系统的上下位机结构。其中CompactRIO 9014具有较好的可靠性和实时性,可容易实现对应变、拉压负荷等信号的测量和伺服电磁阀的控制输出,各模块工作情况如下:
1)NI 9237AD模块用于采集应变信号和连杆拉压载荷信号,其中应变片贴在连杆试件采集位置,应变信号经过应变仪直接连接到NI 9237AD模块;拉压载荷由Interface拉压传感器接入NI 9237模块。
2)NI 9205AD模块用于采集活塞缸上下两缸压力信号,上下两缸压力信号由KISTLER压力传感器采集。
3)NI 9263DA模块输出设定压力信号控制液压伺服阀,实现系统的非对称加载。
4)NI 9401DI/O模块监控试验系统状态信息,包括液压系统电源开关信号,控制柜电源开关信号,液压泵站油压、温度、泄漏、液位信号,相应信号发生故障后指示灯报警。
5)NI 9485SSR模块用于发现故障后切断相应部分的开关确保试验安全。
3.2 软件设计
本试验系统的软件程序是基于LabVIEW图形化编程语言的开发环境,结合CompactRIO嵌入式控制器开发完成。主要实现了液压加载的控制,试验状态的监控,数据的处理。试验系统软件功能结构图如图5所示。
3.2.1液压加载的控制
试验系统的加载控制主要实现三个内容:自动计算连杆载荷、实现非对称正弦波加载、加载载荷的PID控制。
3.2.1.1加载载荷的计算
载荷的计算主要是确定连杆所受的最大压力和最大拉力,以确定非对称正弦波的正负幅值。基于2.1中对连杆受力情况的分析和连杆拉压载荷的推导计算(此处从略),可将连杆划分为小头、杆身、大头三部分计算其最大拉压载荷,代替对所有的截面的计算。简化后的计算方法如下:
(1)最大拉伸载荷下:
小头端:
大头端:
杆 身:
(2)最大压缩载荷下:
小头端:
大头端:
杆 身:
式中 ——爆发压力,Pa
——曲柄转角
——连杆比
=
——曲柄回转半径,m
——连杆大小头中心距,m
——活塞组质量(活塞、活塞环组、活塞销、活塞销卡环总质量),kg
——活塞顶投影面积,
——曲柄运动角速度,rad/s
——计算截面截取至小头端质量,kg
——计算截面所截小头端质心到小头孔中心距,m
——连杆质量,kg
D——缸径,m(此处为近似,当知道活塞顶直径时,用活塞顶直径更加准确)
在选择发动机计算工况时,以发动机最高转速工况作为连杆受力计算工况,同时以发动机最高扭矩的最大爆发压力代替最高转速下的最大爆发压力,会得到比较保守的试验结果。
计算完以上数据后就可以计算平均载荷、载荷幅值和负荷比。
平均载荷:
载荷幅值:
负荷比:
通过以上各数值的比较,尤其是平均载荷的比较,选择大头端、小头端和杆身载荷较大的作为加载载荷。对于确定的加载载荷,可以设定载荷强化系数进行相应的载荷强化。强化后的载荷作为强化试验的加载载荷。
根据以上计算原理,软件采用LabVIEW中的公式节点,实现以上计算。提取该部分程序以某型号的连杆为模型进行计算调试,结果如图6所示。
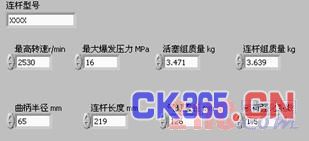
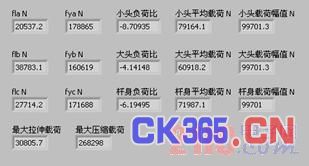
图6:某型号连杆试件拉压载荷计算
3.2.1.2非对称正弦波加载的实现
非对称加载主要通过CompactRIO 9014 FPGA模块的FPGA Memory及CompactRIO 9263模块实现。FPGA Memory可以记录设定点数的数值,并按照顺序记录每个数值的地址,索引FPGA Memory的地址便得到相应的数值;CompactRIO 9263则输出相应电压控制波形对伺服阀进行控制,电压正负控制产生拉伸或者压缩载荷,电压大小控制伺服阀开度进而改变拉伸或者压缩载荷的大小。
具体方法为:
1)制作一个周期幅值为1的标准正弦模拟波形,由1024点组成
2)将模拟波形转换为常量导入FPGA Memory
3)将赋值好的FPGA Memory正负值分别设置正负放大系数
4)把数值输入CompactRIO 9263模块,产生非对称正弦控制波形
以上一节计算的连杆为例,生成非对称波形为:
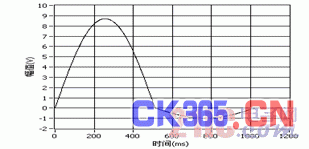
图7:输出控制波形
当为静载试验时,只控制液压缸向一个方向运动,拉伸加载时负半轴都为0;压缩加载时正半轴都为0。
3.2.1.3加载载荷PID控制
PID主要针对动态疲劳试验而言,本试验系统采用常规的PID控制方法。加载载荷为循环非对称拉压载荷,要保证加载载荷达到所设定最大拉伸和压缩载荷值,则最大拉伸载荷和最大压缩载荷即为PID控制的目标值;同时系统采集连杆试件承受拉压载荷信号,并将最大值最为PID控制的反馈量。控制原理如图8所示。
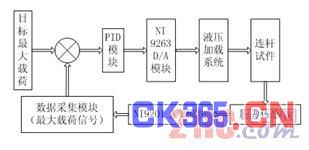
图8:加载载荷PID控制原理图
图9为LabVIEW中的FPGA PID控制模块部分程序图,该模块大大简化了控制过程。只需要设定好各个接口参数,然后将反馈信号连入process variable端口,就能得到相应的输出。
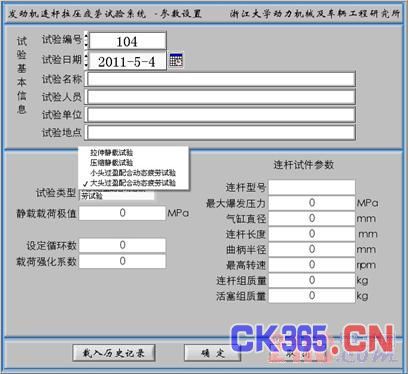
图9:FPGA PID模块部分程序图
加载载荷PID控制仿真如图10和11所示。图10列出对该PID控制模块各参数的设定(PID参数调试过程此处从略)。设定完毕后,将PID模块的Setpoint由0变为14.3,得到响应特性如图11所示。时间单位为每刻度50ms,在,Setpoint(红色)较大变化的情况下,Process Variable(蓝色)在3s内达到Setpoint并保持稳定。
仿真结果说明加载载荷PID控制满足试验系统的要求。同时,响应特性可以通过改变PID参数进行调节。
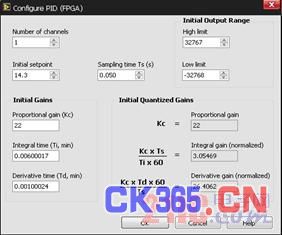
图10:FPGA PID模块参数设置
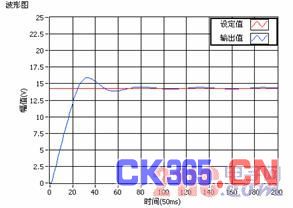
图11:液压加载系统PID控制响应图
3.2.2试验状态的监控
试验状态的监控主要包括疲劳破坏、加载载荷和安全故障三个部分。
3.2.2.1疲劳破坏的监控
疲劳破坏的监控,主要根据CompactRIO 9237模块采集连杆试件相应位置的应变,在监控面板上实时显示应变波形和峰谷值。当超出设定范围并超出设定范围次数达到设定值时,判定连杆发生破坏,试验自动暂停,试验人员进行检查。
3.2.2.2加载载荷的监控
加载载荷监控包括三个方面:连杆拉压载荷监控、液压缸上油腔压力监控、液压缸下油腔压力监控,三个载荷都通过CompactRIO 9201模块采集,在监控界面上实时显示波形图。其中拉连杆压载荷的测量通过Interface拉压力传感器,两个液压缸油腔的压力测量通过KISTLER压力传感器。
3.2.2.3安全故障的监控
保证试验安全是重中之重,本试验系统针对存在安全隐患的部分进行监控,在发现故障后进行相应的处理。这部分是软件通过CompactRIO 9401DI/O模块和CompactRIO 9485SSR模块实现的:CompactRIO 9401DI/O模块实时监视液压系统电源开关信号,控制柜电源开关信号,液压泵站油压、温度、泄漏、液位信号状态,当状态不正常时,由CompactRIO 9485SSR模块切断相应部分的开关,确保试验安全。
3.2.3数据的处理
如图4所示,试验系统针对每种信号都有相应的NI硬件进行采集。CompactRIO 9014的RT和FPGA模块保障了数据采集、监视、存储的实时性和可靠性,LabVIEW的公式节点和XY波形图可对数据进行较好的分析。针对疲劳试验时间长、数据量大的特点,数据的处理采用LabVIEW中的TDMS数据流。
四. 试验系统现场成果
4.1硬件现场效果
4.1.1系统功能
(1)用于发动机连杆拉压疲劳试验,并对试验结果作出相应评估;
(2)可作为发动机零部件静载试验的加载系统;
(3)使用静态应变仪可以测试被试件的应力、应变状态。
4.1.2性能指标
(1)加载形式:拉力压力可连续单独调节,可达到任意负荷比;
(2)压力范围:0~28Mpa,手动调压;
(3)脉冲频率:≤22HZ,连续可调;
(4)加载波形:非对称正弦波;
(5)控制精度:拉压载荷≤4%,加载频率≤2%。
4.1.3组成结构

图12:机械台体实物图
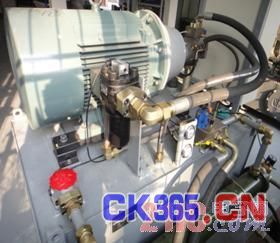

图13:液压加载系统实物图
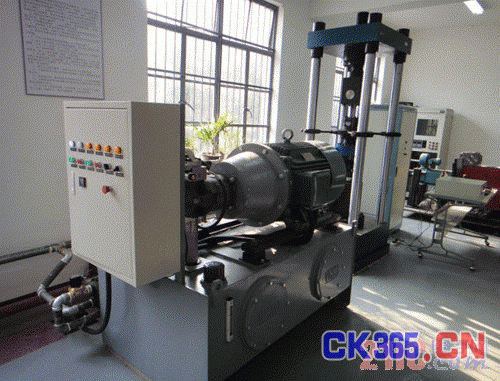
图14:试验系统整体效果图
4.2软件效果
打开程序后,进入了程序主界面,主界面将程序分为三个主要模块:试验设置、实时监测和数据分析。同时还有关于部分介绍试验系统相关信息以及退出系统按钮。

点击“关于”按钮后,出现介绍整个试验系统基本信息界面。
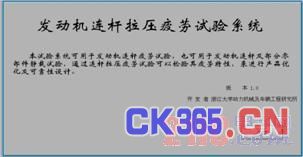
点击“试验设置”按钮后,进入试验设置界面。
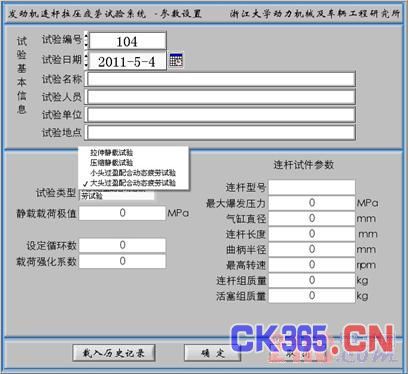
试验设置主要分为三个部分:试验基本信息、试验系统参数和连杆试件参数。设置参数可以手动输入,也可以载入历史记录。选择不同的试验类型(拉伸静载试验、压缩静载试验、小头动态疲劳试验和大头动态疲劳试验)时,与之相应的参数会显示出来进行设置。
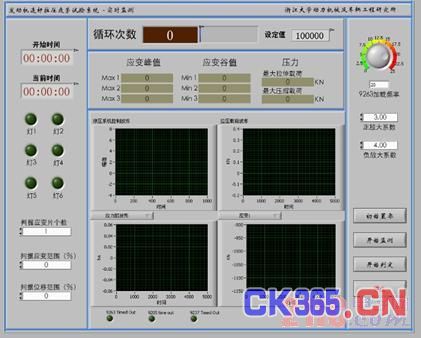
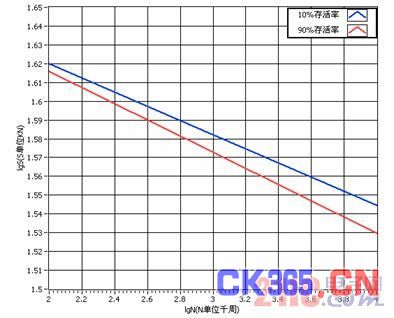
点击“实时监测”按钮时,会出现监测界面。试验监测时,有以下信息:
(1)四个波形图显示控制波形、加载载荷、拉伸压缩载荷(可选择显示)、应变波形(可选择显示);
(2)六个指示灯显示液压系统电源开关信号,控制柜电源开关信号,液压泵站油压、温度、泄漏、液位信号状态;
(3)时间显示以及循环次数显示都是实时显示疲劳试验进行程度;
(4)位移判定范围、应变判定个数及范围都是实时设定监测连杆试件疲劳状态方式;
(5)初始置零消除各传感器无信号时干扰,循环置零使循环数清零;
(6)频率和伺服阀控制信号(正负放大系数)实时可调以调整试验状态;
(7)三路应变的峰值谷值实时显示;
(8)系统拉伸压缩载荷极值显示目前可达到的载荷极值;
(9)连杆所受最大拉伸和压缩载荷实时显示;
(10)NI 9263、NI 9205、NI 9237超时指示灯显示三个板卡超时状态。
点击“数据分析”时,进入数据分析界面,主要有查看数据、开始记录、停止记录和输入数据保存路径。试验时,可以查看数据,根据数据情况控制开始或者停止记录,记录数据时指示灯亮。

在数据分析方面,LabVIEW公式节点和XY波形图,实现对数据的疲劳可靠性分析,可得出相应数据的P-S-N双对数直线,如图10所示。
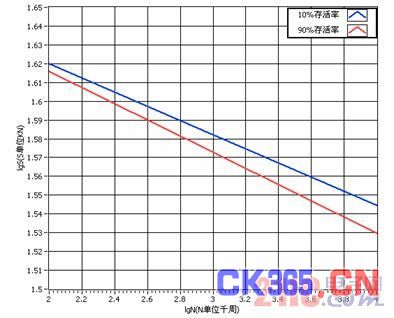
图15:P-S-N双对数拟合直线
基于以上的设计,整个试验系统的试验流程如图16所示。

图16:试验程序框图
五. 结论
1. 所研制的发动机连杆拉压模拟疲劳试验台是国内首个自主研发,拥有自主知识产权的专用试验台。
2. 本试验台基于连杆主要承受拉压载荷的试验原理,采用NI CompactRIO嵌入式控制器和液压加载系统的硬件设计使试验系统具有较高的可靠性、准确性和实用性;结合LabVIEW开发环境进行软件编程,使试验系统开发周期短,扩展性强。
3.本试验台采用非对称加载方式,实现了对连杆实际工况的模拟;液压加载的PID控制实现了载荷的精确控制;同时与实机试验相比,可以实现强化试验,既缩短了试验周期、提高了试验效率,又可以更全面的检验连杆的疲劳性能,对连杆新产品的设计和已有产品的优化有较大的意义。