电磁无损检测是利用材料在电磁场作用下呈现出的电学或磁学性质的变化,判断材料内部组织及有关性能的试验方法。电磁方法检测材料表面具有检测灵敏度高、信号藕合简单、方便等优点,广泛应用于工业生产与科学研究中,是无损检测技术的一个重要分支。目前钢铁件表面加热淬火后硬化层深度(的的测定,通常用金相法(由表面测至50%马氏体区)、硬度法(按半马氏体区硬度为准)和酸蚀法来测定。而这些方法都是破坏性的,无法实现100%检测。本文通过分析磁矫顽力与淬硬层深度之间的关系,试制了一种应用电磁原理、采用微机控制的硬化层深度电磁无损检测仪(DWY一1)。
1检测原理
1.1钢铁材料表面加热淬火后的金相组织
钢铁材料经表面加热淬火后的金相组织与加热温度沿截面分布有关。一般可分为淬硬层(I),过渡层(11)和心部组织(m)三部分,如图1所示。其中第工区加热温度高于弋,淬火后得到全部马氏体组织,称全淬硬层。第11区,加热温度在人:一Acl之间,淬火后得到马氏体十铁素体组织,称过渡层。第m区,加热温度低于Acl为原始组织。
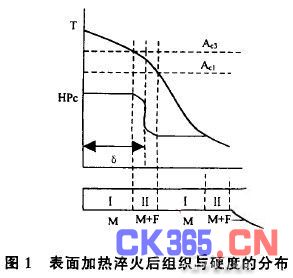
1.2钢铁材料的磁特性
除奥氏体不锈钢外,一般钢都是铁磁性材料,都具有如图2所示表面加热淬火后组织与硬度的分布的磁特性。一些表示磁特性的参数,如磁感应强度、磁导率、矫顽力等都与金属及合金的晶粒大小、形状、第相分布相关。钢铁件经过热处理后,组织结构发生变化,磁性参数也随之变化。大量实验证明,如将不同含碳量的钢,经不同热处理后,测量各磁性参数和硬度、含碳量之间的关系,便可发现矫顽力和含碳量、硬度关系为最好。从图3所示碳钢的硬度、矫顽力和含碳量之间的关系曲线,可以看出,硬度和矫顽力都随含碳量增高而上升。其中当碳钢的含碳量小于或等于0.6%时,在相同的热处理条件下,矫顽力Hc与钢的含碳量成正比,当含碳量大于0.6%时,矫顽力HC与钢的含碳量成单值对应关系,当回火温度低于300℃时,不同成分的碳钢经不同的热处理后,其硬度和矫顽力之间基本上呈直线关系,见图4。
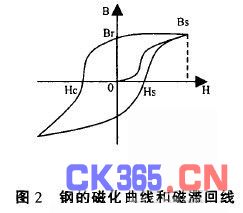
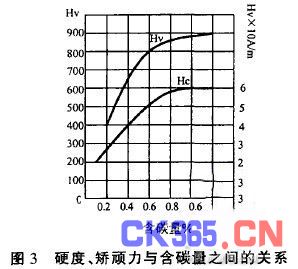
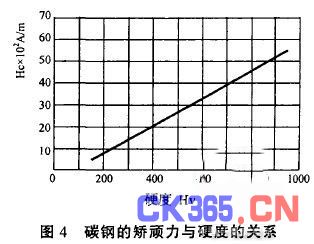
1.3电磁检测原理
由金属及合金的铁磁性可知,马氏体的矫顽力为最高,珠光体次之,铁素体为最低。因此,可以通过测量工件淬火后的矫顽力来检测淬硬层的深度。
磁性检测仪的磁路模型如图5所示,在被测工件的表面上放置一个门字型的电磁铁,电磁铁中间放置霍尔元件,用以测量磁路中的磁通量,当磁化线圈通过直流电后,电磁铁与被测工件便组成一个闭合磁路。测量时先用饱和励磁电流Im将工件局部磁化,然后通人反向退磁电流Ic,当反向电流增加到使磁感应强度Br=O时,测出此时对应的反向电流值Ic,根据安培环路定律,可列出如下方程:

式中:Fc一总磁势;
N一探头电磁线圈匝数;
HcZ一淬硬层的矫顽力;
Ic一反向电流强度;
Hcl一探头电磁铁的矫顽力;
Hc3一未淬硬部分的矫顽力;
占一淬硬层部分磁路长,即淬硬层深度;
Ll一探头电磁铁的磁路长;
L3一未淬硬部分的磁路长;
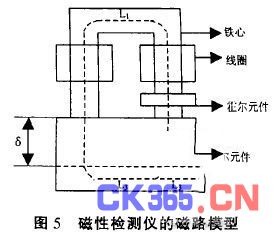
当工件未淬火时(1)式为:

因此:

其中:} H}z一Hc3)对于相同钢种,相同热处理条件的同种工件为定值,其值可通过实验测得。因此,与8成线性关系,通过测量△I。值便可测出淬硬层深度8值。
测试系统原理框图如图6所示,由微机控制整个系统的检测过程和数据处理。

2 检测方法
2.1原材料平均1的测定
表面淬火前,我们将所有工件进行逐件检测、分组,并计算每组平均Ic。这样不仅可测定每组平均I。值,而且可以通过分组解决相同牌号不同炉号钢材的电磁特性相差较大而造成的测量误差,同时通过检测还可进行混料分选。
2.2表面淬火后Ic‘的测定及占值的确定
表面淬火后我们用同样的方法对工件进行逐件检测,测出每个工件的Ic、值。并由△Ic、Ic(Hc:一Hc3)确定每个工件的淬硬层深度占值。
3实例
根据上述原理,我们设计了一台电磁无损检测仪(DWY一1)。用于对某厂生产的曲轴进行淬硬层深度无损检测。该曲轴材料为47MnTi感应加热淬火,180一220℃低温回火后要求到HRc45处淬硬层深度为5-5.smm。我们在生产现场任意抽取工件20件。首先采用硬度法即用显微硬度计测硬度法测量淬硬层深度,然后用DWY一1型电磁无损检测仪进行测量,结果见表1。可以发现测量误差不超过0.Zmm完全满足生产的需要。

4误差分析
产生上述测量误差的主要原因为,工件经热处理后产生变形,导致工件与探头铁心之间出现间隙;工件在机加工过程中产生尺寸偏差,使得工件与探头铁心接触不够紧密;工件的表面质量不佳,如存在氧化皮、铁锈等。由于空气隙的磁导率远远小于铁心和工件的磁导率,所以空气隙处的磁阻很大,影响了反向电流Ic的值。
5结论
基于矫顽力研制成功的DWY一1型电磁无损检测仪能实现淬硬层深度的无损检测且能满足生产的需要。