为获得高质量的石油加工产品或增加原油转化为轻质成品油的比率,以及适应高含硫原油、劣质原油深加工的需要与改善环境条件等目的,在现代石油加工工业中出现了加氢工艺装置[1]。与此同时,加氢装置中的关键设备加氢反应器的设计及制造技术也有了很大的进步。自20世纪70年代以来,为适应炼油工艺改进(主要涉及催化剂和反应温度等的变化)的需要,在炼油化工行业中热壁加氢反应器已逐步取代了冷壁加氢反应器。
热壁加氢反应器在制造和安装过程中,铬钼钢焊缝以及不锈钢堆焊层将不可避免地出现一些表面或近表面缺陷;在使用过程中,由于其长期在高温(400~500℃)、高压(8~20 MPa)以及临氢状态等苛刻条件下工作,将产生堆焊层的表面开裂和氢致剥离以及母材的回火脆化和氢脆。针对这些缺陷,铬钼钢焊缝表面、近表面缺陷可采用磁粉和磁记忆检测,主体焊缝埋藏缺陷应采用射线、超声波检测,内壁不锈钢堆焊层表面缺陷应采用渗透检测,对于堆焊层内及层下缺陷应采用超声波检测。目前国内对加氢反应器主体焊缝主要采用射线检测或射线加超声波检测,国外对加氢反应器主体焊缝采用超声波TOFD技术进行检测。
1 加氢反应器制造过程中的质量控制
加氢反应器筒节、接管和法兰等原材料均为锻件,锻造时易产生裂纹、夹层、折叠和白点,锻后热处理易产生再热裂纹缺陷。
由于高强度铬钼钢的可焊性较差,焊后将在主体对接焊缝以及工卡具焊疤处不可避免地出现一些表面、近表面或埋藏缺陷(如裂纹、未熔合、未焊透、气孔、咬边和夹渣),尤其是焊后延迟裂纹类危害性缺陷。
内壁不锈钢双层堆焊层缺陷按出现部位可分为四种,即①表面缺陷,包括裂纹、气孔、划伤和夹渣等。②堆焊层内的缺陷,一般为夹渣和未熔合。③堆焊层与母材的未结合。④堆焊层下的再热裂纹。
堆焊层表面裂纹主要产生在手工焊双层堆焊处。由于手工堆焊工艺较自动堆焊难于控制,焊接过程中产生的σ相造成E347焊缝金属的延性降低,在局部应力集中或焊接残余应力、热应力的作用下会产生裂纹,成分和金相组织的偏析是产生裂纹的重要因素[2]。
1.1 射线检测
对于铬钼钢,为避免漏检焊接延迟裂纹,应在焊接热处理24 h后进行射线检测。加氢反应器主体焊缝多为厚壁窄间隙焊,考虑射线的能量,通常采用两种方法进行射线检测,即①壁厚<200 mm时实施60Co源γ射线检测。②壁厚≥200 mm时实施直线加速器检测。
射线检测易于发现坡口未熔合等与射线束平行的缺陷,但对于厚壁焊缝射线底片清晰度差。
1.2 超声检测
1.2.1 原材料锻件的超声波检测
应在热处理后,槽、孔、台阶加工前进行。主要检测与锻造方向垂直的面状缺陷,对于筒节、接管应从外壁进行100%扫查,对于法兰沿法兰面进行100%扫查。筒节的检测灵敏度可用底波计算法确定;接管和法兰可直接采用试块法确定。横波检测时使用K1探头,从筒节外壁沿四个方向进行扫查,以检测筒节内外壁表面缺陷,扫查覆盖率应为探头宽度的15%以上。灵敏度的选取,在具有内外V型沟槽的筒型试块上进行调节,绘制距离-波幅曲线。
1.2.2 主体对接焊缝的超声波检测
焊后、热处理后和水压试验后对主体对接焊缝进行三次100%超声波检测。首先使用单晶直探头对斜探头声束通过的区域进行检测,然后使用K1.0和K1.5横波斜探头进行两次重复检查。对于可疑部位,应进行手工串列扫查,以检出垂直于表面的缺陷。
1.2.3 堆焊层内及其与母材未结合处的缺陷检测
对于筒体、封头等形状较为简单的工件,使用5N14窄脉冲直探头从外壁检测堆焊层内的缺陷以及堆焊层与母材的未结合缺陷。当需要精确定位和定量时,应从堆焊层侧进行复探。对于接管、凸台等形状较为复杂的工件,使用双
晶直探头从堆焊层侧检测堆焊层内的缺陷以及堆焊层与母材的未结合缺陷。
对于双晶直探头,要求两声束间的夹角应满足有效声场覆盖全部探伤区域,并能使探头对该区域具有最大灵敏度。换能器总面积≯325 mm2。从堆焊层侧探伤时,探头最小探测深度应达到1 mm。
执行标准为JB/T 53701—1993加氢反应器堆焊层的超声波探伤。
1.2.4 堆焊层下的再热裂纹的检测
这种裂纹主要产生在堆焊层下的母材中,一般成群出现,位于焊带之间凹槽周围约10 mm的区域,裂纹方向垂直于表面且垂直于堆焊方向,裂纹长度<10 mm,深度为堆焊层下1~2.5 mm不等,相邻裂纹之间的间隔为2~10 mm[3]。
随着工件厚度的增加,缺陷信号的分辨会更加困难,因此对于堆焊层下的再热裂纹的检测,应使用频率2MHz,折射角为70°的纵波双晶斜探头从堆焊层侧进行检测。试块的形状和尺寸如图1示。
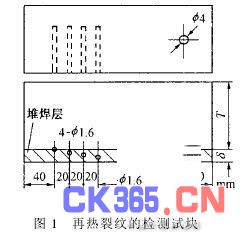
1.3 磁粉检测
主体对接焊缝在角焊缝焊后、热处理后和水压试验后必须进行三次100%磁粉波检测。使用旋转磁场或磁轭法进行磁化,使用磁轭法时至少应在两个相互垂直的方向进行磁化,外壁焊缝一般使用黑磁粉,内壁焊缝使用荧光磁粉。执行标准为JB 4730—1994。
1.4 渗透检测
堆焊层表面裂纹常产生于手工堆焊处,如接管周围手工堆焊部位和返修部位。因此应重点对这些部位进行检测,渗透检测时,应严格控制氯离子含量,最好使用核级渗透剂。
2 反应器定期检验
加氢反应器的主体材料一般为2.25Cr1Mo,内壁堆焊E309(过渡层)和E347(表面层),设计壁厚在80~240 mm(包括锻焊结构和板焊结构),设计压力8~20 MPa,设计温度400~500℃,工作介质主要是氢、油和硫化氢等。
在使用过程中,由于热壁加氢反应器长期在高温、高压以及临氢状态等苛刻条件下工作,面临氢腐蚀、应力腐蚀、介质腐蚀、氢脆、回火脆化和蠕变脆化等一系列问题,材料会趋向劣化,产生堆焊层的表面开裂和氢致剥离以及母材的回火脆化和氢脆,材料的脆化、塑性转变温度向高温区移动。停车检修期间由于水分带入容器内,产生连带硫酸应力腐蚀。
研究表明2.25Cr1Mo钢在370~565℃时会发生回火脆化[4],热壁加氢反应器操作温度正处于回火脆性敏感温度区域,因此一般认为热壁加氢反应器2.25Cr1Mo钢发生回火脆化是不可避免的。
由于筒体母材和焊缝的回火脆化,造成韧性降低,焊缝中一些较小的缺陷就有可能得到较快的扩展而引起反应器失效。因此对于主焊缝来说检验问题变得十分突出,其检测要求也比较高。
2.1 渗透检测
反应器使用一段时间后,内壁堆焊层表面结了一层约0.2mm厚的较坚硬的具有金属光泽的铁碳化合物,对其进行轻微打磨后即见光泽,易误认为金属本身而使得渗透探伤误操作。因此,停车开罐检验时,为有效检测出堆焊层表面缺陷,渗透检测时必须清除堆焊层表面污垢,使之现出金属光泽。
2.1.1 检测部位
根据大量的检验结果表明,堆焊层的表面裂纹通常在以下部位产生:反应器支撑凸台、法兰密封槽部位;铁素体含量超标的部位(往往是返修部位)及接管周围手工堆焊部位。因此,以上部位是加氢反应器检验的重点部位。
2.1.2 渗透剂的选用
为防止不锈钢卤族元素的应力腐蚀开裂,应选择核级渗透剂。如有必要可利用金相检验以发现渗透检测无法检出的微裂纹。
2.1.3 缺陷的处理
表面裂纹一般应打磨处理,对于较深的裂纹可用超声波测定裂纹的深度(扩展到347与309界面的裂纹应重点予以检查)并采用金相方法进行分析,因焊接返修工艺难控制,非有必要,一般不返修。
2.2 磁粉检测
鉴于在役热壁加氢反应器铬钼钢的回火脆化特性,表面缺陷的存在使得焊缝应力集中程度增大,因此应从外壁对主体对接焊缝以及角焊缝进行100%磁粉检测。
使用便携式磁粉探伤机以旋转磁场或磁轭法进行磁化,使用磁轭法时应至少在两个相互垂直的方向进行磁化,一般使用黑磁粉。执行标准为JB4730—1994。
2.3 超声检测
2.3.1 主体对接焊缝的超声检测
(1)检测部位 主体对接环焊缝、热电耦接管焊缝、冷氢接管焊缝、卸剂接管焊缝。
(2)检测方法 ①从筒体外壁使用直探头和斜探头检测。②使用单晶直探头对斜探头声束通过的区域进行检测。③使用K1.0和K1.5横波斜探头对焊缝进行两次重复检查。④对于可疑部位,应进行手工串列扫查,以检出垂直于表面的缺陷。
(3)缺陷的超声波端点衍射测高技术 ①适用常规超声波探伤所检出的缺陷测高。②一般使用单聚焦斜探头,选择一次波法测定缺陷的高度,探测面应尽量在焊缝的一面两侧。③灵敏度选择时,选择缺陷回波幅度最高的位置进行测定,在适当的灵敏度下扫查缺陷并辨别端点衍射波信号。测高时应在端点衍射波信号幅度达到满屏的10%且整屏无噪声信号的灵敏度下进行测定[5]。
2.3.2 氢致剥离缺陷的超声波检测
(1)堆焊层氢致剥离的产生 堆焊层的剥离是一种氢致延迟开裂现象。由于反应器在长期运行过程中开、停车的升温与降温,使氢在熔合区的不锈钢堆焊层侧聚集,再加上热应力及熔合面上淬硬组织的影响,当熔合线界层上氢聚积达到相当浓度时则产生氢致剥离。
(2)检测面的选择 考虑内壁为带极自动堆焊,带极间存在沟槽;而外壁母材较为平整,探头与器壁耦合明显优于内壁,且在确定检验部位及对原有缺陷复核时定位容易。因此堆焊层剥离的超声波检测应在母材侧进行。
(3)检测部位 温度、压力波动较大区域(如冷氢段);内壁制造时返修较多的部位;停车降温时,温度下降较快、厚度较小的封头处等为检测重点。
(4)检测灵敏度的选择 按JB 4730—1994选择检测灵敏度10%~80%作为基准灵敏度,检测时应在反应器筒体上进行灵敏度的调节,以减少标准试块和容器筒体晶粒度差异所造成的误差。
2.3.3 堆焊层层下裂纹及表面裂纹的超声检测(不卸剂检测)
(1)堆焊层层下裂纹的超声波检测 使用2·5P13×13K1纵、横波斜探头在图1试块上进行灵敏度调节,从反应器外壁分别采用K1纵、横波斜探头沿平行于带极堆焊方向和垂直于带极堆焊方向进行检测。
(2)堆焊层表面裂纹的超声波检测 采用单斜探头检测时,对JB 4730—1994中T2试块进行改进,在堆焊层表面周向和轴向分别加工不同深度的矩形槽缺陷。使用2.5P13×13K1纵、横波斜探头在该试块上进行灵敏度调节,从反应器外壁分别采用K1横波斜探头,K1纵波斜探头沿带极堆焊方向和垂直方向进行检测。为克服奥氏体不锈钢堆焊层超声波检测的诸多不利,运用超声波爬波技术、缺陷衍射波方法,对堆焊层缺陷(堆焊层表面、层下裂纹)外壁进行超声波检测,以替代内表面的渗透检测,检测原理如图2。
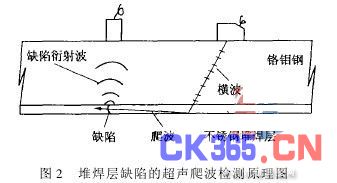
2.4 金属磁记忆检测
接管以及高应力部位应进行金属磁记忆检测,以检查应力分布情况,必要时进行磁粉检测复验。
3 加氢反应器在线监测的无损检测技术
由于加氢反应器长期在高温、高压以及临氢介质等苛刻环境条件下工作,将不可避免产生铬钼钢回火脆化以及堆焊层的剥离及开裂现象,考虑加氢反应器长效运行,在日常运行中应对这些缺陷进行在线监测。
3.1 超声波监测技术
对于已知的缺陷,应使用常规超声波检测技术以及超声波端点衍射测高技术从外壁进行定期监测,以查明该缺陷在长度和高度方向上的扩展情况。
3.2 声发射监测技术
使用声发射技术进行在线监测,将探头通过高温传感器布置在反应器器壁上,监测开、停车期间堆焊层产生的缺陷活动情况。对有意义的活动源,应采用超声波检测技术进行详细测定。
4 小结
(1)无损检测技术对加氢反应器安全运行极其重要。
(2)制造过程中,锻件质量以超声波检测方法为主,堆焊层的表面质量采用渗透检测方法,对接焊缝的检测用射线或超声检测方法进行。
(3)对于在用过程的定期检验,以表面检测和超声波检测方法为主。另外,声发射检测和磁记忆检测等新技术在在线监测方面已开始得到应用。可以预计,随着新的无损检测技术的发展,必将有一些检测速度更快、灵敏度和可靠性更高、缺陷显示更直观的新方法在加氢反应器的检测中得到应用。