1引言
PLC广泛应用于工业控制领域,因其具备良好的扩展性和独有内部逻辑的二次编程功能,大大扩展其在工业生产和工业控制领域的应用范围。本文从电力系统智能装置的自动测试系统原理出发,简要介绍自动测试系统结构,详细介绍PLC在本系统功能和具体应用,并针对PLC在电力系统智能装置自动测试系统特殊领域的应用中出现的触点检测的条件、采样数据上送和特殊控制逻辑的要求问题进行讨论,并给出一般解决办法。实践应用表明,可编程控制器的良好的扩展性和其独有逻辑编程特点有效扩大其应用领域和范围。
2系统基本原理
电力系统智能装置一般包括是继电保护装置和测量控制装置。继电保护装置主要功能是保护电力系统的一次设备安全运行,确保电力系统输电系统的安全运行,而测控装置主要负责电力系统开关的控制和电气量的测量,二者构成完整电力系统二次保护设置。
从电力系统智能装置和外部一次设备的发生联系的主要电气量包括:一次设备的模拟量、一次设备的信号开入和继电保护出口三个最主要部分。因此,模拟现场运行环境的电力系统智能装置自动测试系统也必须具备模拟量输出、开关量输入和开出触点的检测功能,但不仅仅限于这三部分的功能的检测,其他还应包括时钟同步等等功能的检测。
目前,电力系统智能装置是属于微机型,其具备完好信息记录功能,具备和其他外部系统良好的信息交换功能。因此电力系统智能装置的自动测试系统应包括四个最主要的功能:用于模拟故障模拟量输出模块、提供保护装置开人的开入模块、用于检测保护装置动作接点的开出检测模块和装置信息的解析模块。电力系统智能自动检测系统的基本原理:通过专用设备模拟电力系统故障状态模拟量输出,并通过开入模块提供保护装置的开入量,从而满足保护装置保护动作基本条件,通过解析保护装置的信息和检测保护装置的动作出口触点,从而完成保护装置的基本功能的检测任务。
3系统组成和各模块基本功能
从电力系统智能装置的自动检测系统原理的出发,一个完整的电力系统智能装置的检测系统包括:微机继电保护测试仪、保护装置的开入模块、保护装置的触点检测模块和控制计算机模块。自动检测系统它主要由测试控制计算机、微机继电保护测试仪、可编程控制器、被测智能装置构成。
微机继电保护测试仪接受自动测试控制平台发出控制参数及命令类型,向保护装置输出模拟量,完成向保护装置输出模拟量完成保护功能的测试,并及时将测试仪器反馈信息以标准统一格式上报到自动测试控制平台。
可编程控制器根据自动测试控制平台发过来的命令,输出开关量信号,实现保护装置硬压板的控制和保护开关量输出功能,将基于保护装置继电器开出触点检测输入的采样数据,上送自动测试控制平台,为保护动作触点判断提供连续有效开入量采样数据。
测试控制计算机是整个控制系统的核心硬件,它通过网络和系统中其他硬件进行信息交互,控制继电保护测试仪向保护装置输出模拟量,接收保护装置信息解析模块上送的保护动作信息并通过其完成对保护装置的控制,控制可编程控制器输出保护测试的开入量命令,检验保护装置继电器开出触点动作。
微机继电保护测试仪选用北京博电PW30AE,可编程控制器选用GE公司的GE-9030,可编程控制器通讯模块使用以太网模块。
4 PLC应用主要问题及解决办法
可编程控制器在本系统的任务是完成智能装置的保护出口继电器触点或者遥控触点的检测和智能装置的遥信开入检测,具体到可编程控制器各模块是开入模块负责检测出口继电器触点导通和开出模块负责提供开出完成智能装置的遥信的检测功能。同时为了交换信息的需要,可编程控制器必须配置相对应的通讯模块以满足可编程控制器和上位机信息交换要求。
在本系统设计时,对开入模块的功能有具体的要求,这些要求是和电力系统的智能装置实现的功能是密切相关,如触点类型和触点的导通时间等,因此必须分析智能装置的保护出口继电器触点和遥控触点检测的具体要求,并以此为要求进行可编程控制的硬件选择和内部逻辑回路的设计,充分满足本系统对触点检测的特殊要求。可编程控制器的开出模块逻辑回路的设计也必须满足本系统的特殊需要。
4.1继电器出口触点检测特殊要求
可编程控制器开入模块负责检测继电保护出口继电器辅助触点的通断情况,并将开入模块数据上送到控制计算机,并作为控制计算机自动检测成功标准之一。
因此可编程控制器开入模块检测功能的强弱决定本系统的可靠性和稳定性。
继电保护装置的出口继电器触点包括四类:保持型常开接点、保持型常闭节点、瞬动型常开接点和瞬动型常闭节点。对于保持型出口触点的检测来说,可编程控制器的开入是满足自动检测的需要。而对于瞬动型触点的检测,可编程控制器开入模块检测功能是否满足要求取决于PLC本身扫描周期T1和瞬动接通的时间T2两者的关系。考虑到可编程控制器由于扫描方式引起开入延时最长可能达两个扫描周期,如果保护装置的瞬动触点的接通时间T2大于两倍的扫描周期T1,该触点的状态变化就可以被PLC开入模块所检测到。
瞬动触点的接通时间取决两个因素,一是装置软件内部对瞬动继电器出口延时整定的时间,目前各厂家提供的技术参数来看,装置软件触点延时的时间一般设置为50-100毫秒,二是出口继电器本身动作时间和断开时间参数也会影响瞬动触点的接通时间。假设瞬动型触点的接通时间为100毫秒,要求可编程控制器的扫描周期的时间小于50毫秒,才能保证可编程控制器的开入模块的检测功能的有效性。
可编程控制器的扫描周期和可编程控制器的硬件参数和用户的程序的大小有密切的关系。因此只要通过硬件配置和相关技术手册提供的技术参数并结合用户的PLC程序指令类型和各指令类型数目计算出可编程控制器扫描周期,选择合适可编程控制器模块,保证可编程控制器扫描周期小于50毫秒,保护装置的瞬动型触点检测就可以在可编程控制器开入模块来完成。
4.2上位机数据采样特殊要求的实现
在前面小节中,讨论了可编程控制器必须满足检测保护装置的四类节点的检测的基本条件。但前面条件的符合,只能保证PLC开入模块能够检测保护装置动作触点状态的变化情况。在自动测试系统设计中,可编程控制器的开入模块仅仅采集触点状态,而完成触点状态检测标准判断是在控制计算机中完成,如何保证上位机能够得到完整、连续的基于采样周期为50毫秒可编程控制器开入模块采样数据是本系统必须要解决的关键问题。
电力系统智能装置自动测试系统检测的对象是继电保护设备中出口继电器动作情况,由于继电保护设备的动作的快速性,部分保护动作时间实现小于50ms,因此部分出口继电器触点状态在较短的时间会出现反转,根据系统设计要求,要求上位机能将保护动作前和保护动作后出口继电器接点动作情况进行检测处理,并将动作前后出口继电器接点状态作为该系统中继电器接点检测判断依据。因此,要通过上位机和可编程控制器通讯数据交换,实现采样时间间隔不大于50ms可编程控制器开入采样数据上送到上位机的目标。
目前,上位机获得可编程控制器的开入采样数据是通过通讯交换信息得到,而提高上位机和PLC数据信息交换效率是解决数据采样的实时性的措施之一,但仅仅依靠提高上位机和PLC数据交换速度是无法到达采样数据周期50ms指标要求,即使上位机使用以太网介质能达到此要求,也会占用上位机比较多资源。同时由于可编程控制器扫描工作方式的特点,通讯模块频繁和上位机数据交换会影响可编程控制器其他模块功能执行,如影响可编程控制器扫描周期。
对于可编程控制器来说,在其内部实现50ms 采样周期的数据采样是完全可以的实现的,充分利用可编程控制器中数据转存和逻辑控制功能, 将每50ms 一次采样数据寄存到连续但不相同数据缓冲区。通过采样周期时间的整定,结合上位机和可编程控制器通讯协议的最大数据长度,上位机只需要在给定的时间内进行一次读取多次采样数据即可。上位机读取采样数据后,根据PLC 采样数据转存的原则和逻辑,将已接收到采样数据进行采样时序的还原即可。
4.3 可编程控制器顺序开出的实现
可编程控制器开出模块顺序开出主要是满足电力系统测控装置的遥信检测要求, 设计具体要求为: ①上位机下发一次命令,启动顺序开出,PLC 接受命令启动顺序开出逻辑回路,由可编程控制器本身完成开出模块开出接点顺序开出。②在顺序开出过程不允许同时出现两个开出同时接点接通状态。③顺序开出执行一次完毕即可停止开出。
设计基本思路: 在启动命令后, 启动维持一个扫描周期时间的定时T1 脉冲信号回路,同时启动另一个计时器T2(T2< T1)。在一个扫描周期脉冲到来时,由设定计数器和目标进行比较, 决定开出继电器序号, 开出执行并保持时间T2 后,计数器加一和执行复位判断程序, 等待下一个脉冲到来后执行上一过程直到全部执行完毕。
设计维持一个扫描周期时间的定时脉冲信号,定时的时间参数为两个开出之间的时间。一个周期定时脉冲梯形图如图1 所示。通过修改定时器类型和计时器参数,确保M100 能够在T1 的时间后产生一个能够维持一个扫描周期间的脉冲信号, 是一个通用的标准的定时脉冲信号程序。M103 为定时脉冲到来后宽度为T2 脉冲。
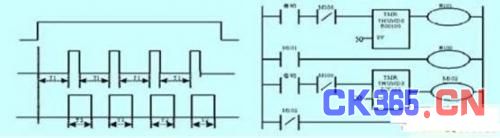
图1 定时脉冲信号程序和梯形图
在定时脉冲到来时, 通过数据比较程序, 由计数器R500 当前值和特殊指定值比较进行逻辑判断,决定是否接通中间继电器,再由该中间继电器决定控制特定的开出,并在自保持回路中串联一个M103 中间继电器触点状态,以控制开出维持的时间。数据比较驱动程序和梯形图如图2 所示。
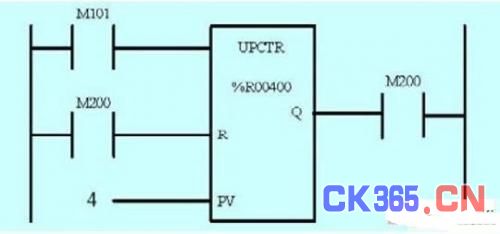
图2 数据比较驱动程序和梯形图
执行一次开出后, 执行计时器计数和复位程序, 本文中使用M00400-M00404 分别控制第1 个到第5 个开出的执行, 每次执行开出后均进行计数器自加一, 并通过计数器逻辑回路进行计数器复位。计数器复位后立刻复位启动线圈,结束本次顺序开出控制任务执行。计数器计数和复位梯形图如图3 所示。
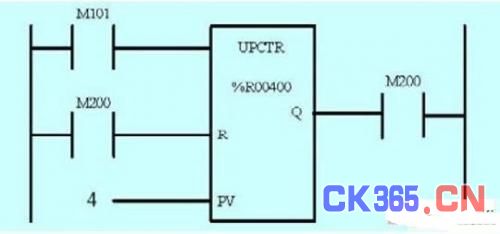
图3 计数器计数和复位梯形图
通过以上控制逻辑的设计,实现启动顺序开出功能的实现, 并实现系统要求一次启动, 按照循序开出不重叠。
通过此逻辑的实现,可以简化上位机在进行遥信检测的控制逻辑, 充分利用可编程控制器开入开出二次编程功能,在不影响可编程控制器性能指标上,减少上位机和可编程控制器的控制命令的交换, 提高上位机遥信的检测效率。
5 结束语
在本系统设计中, 充分利用可编程控制器模块化的组合特点以及其独有开入开出二次逻辑编程的优点,保证系统设计功能的实现的同时, 减少系统主控制平台的在开入和开出功能检测资源开销, 并带来系统稳定性和可靠性。可编程控制器独有可编程的特点为其在工业领域的应用奠定坚实的基础,随着计算机技术的进一步的发展,特别可编程控制器的核心模块CPU 运算的速度得到提高,通过提高指令的执行速度和扩展其计算功能,可编程控制器在工业控制领域的应用会越来越广泛。