介绍在controx(开物)2000的平台上开发设计性能优越的数字控制系统,以实现对某企业的调浆配料生产过程控制。系统设计思路明确、方法独到,而且具有控制精度高、适应性强、可靠性良好等特点,很好地实现了厂家的控制要求。
1 控制系统设计原理
1.1 系统控制过程及要求
企业的主要生产工艺流程为:将铁红厂细磨后的铁红浆料用输料泵输入浓缩机;在浓缩机中进行脱水处理后再储备下来;再采用自动化检测控制技术将高浓缩溶液(浓度值高于60%)通过输料泵输入到混合调制搅拌桶中;在搅拌桶中加水搅拌混合,进行调浆处理(调浆浓度50%, 精度要求5%),调浆后的溶液总量要达到预定值;最后控制输料泵将调浆后的溶液按照预定量输出到标定池中,再进行后继处理。
系统的控制要求是:根据工艺要求,自动调控被控参数,启停各类设备;自动存储历史数据和打印报表;实时显示主要运行参数和曲线;搅拌桶中调浆浓度为50%, 精度为5%;每天出矿量达到T吨,精度为0.3%。
1.2 系统的设计方案
分析系统控制要求,难点主要在于调浆过程和出浆过程的精度控制。调浆过程的浓度精度要求为5%,由于浓度计、密度计等仪器的精度基本在1%-5%之间,所以通过这些仪器可以实现控制精度要求。而出浆过程中精度要求为0.3%,所以出浆过程控制要通过精度更高的仪器来实现,如压力计(精度最低达0.05%)。
根据生产的控制要求,分析系统控制的难点,将系统的控制过程分成浆料浓缩控制过程、搅拌调浆控制过程、出料控制过程三大部分。
1) 浆料浓缩控制过程负责控制启停浓缩机,对铁红厂出来的细磨铁红浆料进行浓缩;并根据浓度计抽样值控制浓缩机出浆开关,以确保从浓缩机出去的溶液是高浓度溶液。此控制过程的控制点只有两个:浓缩机的启停电机和出浆阀门,控制过程相对简单。
2) 搅拌调浆控制过程主要控制加水。由于企业对调浆浓度的精度要求并不高,所以加水量是以搅拌桶进浆开始10min 内溶液的平均浓度为依据计算出来的。
搅拌调浆控制完成之后,搅拌桶内的矿浆溶液浓度在50%左右,桶内溶液高度达到预定的液位计高度。
3) 出料控制过程是最为关键的一步,控制的原理如下:
首先, 通过加油机向搅拌桶中灌入自来水, 每次灌入2000L, 通过对压力计抽样标定对应的水压P2,分别得到2000L、4000L、6000L、…、100000L等50个水压值,并存入系统中。10万升水溶液高度对应的位置就是液位计的位置。
其次,调浆完成后、出浆之前对溶液进行充分搅拌,搅拌时间为预定值。搅拌均匀后,从压力计抽取溶液在液位计高度对应的压力值P1。
最后,系统启动出浆开关,并不断循环抽样检测压力计,抽样间隔为1s。当抽样值达到计算出的剩余矿浆压力值时停止出浆,同时关闭各类设备,系统控制过程结束。
上述方案有如下的优点:充分利用了压力计的高精度性能,确保系统的控制精度要求;各个模块独立,互不干扰,便于操作和维护;避开使用价格昂贵的密度计等仪器,通过使用压力计等仪器降低了系统的费用。
根据生产的控制要求,系统单生产线的控制结构图如1 所示。
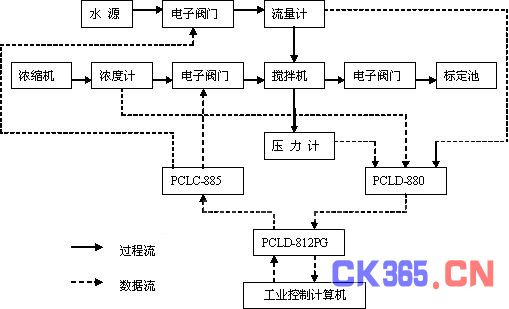
图1 系统控制结构图
2 控制系统设计实现
2.1 控制系统硬件结构
系统中各个物理参数的测量选用相应的传感器来检测,浓度计选用兰州同位素仪表厂的HT-2310, 精度为1% ;流量计选用西安仪表厂的W3000-0401211-100,精度为2% ;压力计同样选用西安仪表厂的315/AGS5S22M, 精度为0.2% ;搅拌转速以及送浆速度、出浆速度的控制选用艾默生的TD1000系列变频器;数据采集卡选用研祥的PCL-812PG,通过它实现控制数据的A/D、 DI 转换;考虑到PCL-812PG的输入、输出信号要求为0-5V电压或4-20ma 电流,而这些信号不满足传感器输出、驱动开关设备的要求,这就需要通过PCLD-880和PCLD-885做中转,对信号进行整流。系统上位机选用研祥生产的IPC-810/PV工控机。
2.2 控制系统软件构架及各部分功能
系统软件的软件构架如图2 所示。为开发生动方便的操作界面,在上位机中采用了国产组态软件,Controx2000 进行控制界面的设计。ControX2000是基于Windows98/2000/NT操作系统的软件包,它内部采用Client/Sever体系结构, 对众多的现场控制器和其他现场智能部件能进行实时控制和监视,操作时具有高性能和高可靠性,以及随时对各种突发事件做出反应,不丢失任何数据和报警信息。
此外,Controx2000与数据采集卡之间的通信无需编制通讯程序, Controx2000将现场的硬件设备采集来的数据通过组态软件的设备驱动程序传送到组态软件中。在ControX2000中只需配置这些硬件的驱动程序, 比如对数据采集卡PCL-812PG, Controx2000就要配置该硬件相应的驱动程序。而在控制系统中,就可以通过设置不同地址的标签量来与数据采集卡的通道相对应,通过标签值的变化反应、控制数据采集卡通道的输入和输出。
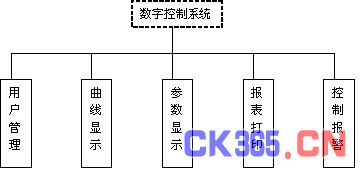
图2 系统软件构架
系统各个功能模块相互独立,互不影响,一定程度上保证了系统的稳定性。其中参数显示模块和报表打印模块有良好的人机交互性能,方便用户实时有效地控制管理生产现场。
2.3 控制系统的主程序框图
按照系统的控制结构图,系统程序控制分成三个控制阶段:浓缩进料过程、加水调浆过程和出料控制过程。
浓缩进料控制过程:人工启动浓缩机进料开关,启动浓缩机搅拌电机开关,系统开始浓缩机进料过程。当浓缩机灌满后,停止进料开关和搅拌电机开关;根据生产需要,启动浓缩机出浆开关、出浆软管泵,在出浆的过程中,数据采集卡实时检测浓度计的抽样值,系统根据采样值判定出浆溶液是否为浓度大于60%的高浓度溶液。如果判定为否,关闭出浆开关和软管泵。
加水调浆控制过程:在启动浓缩机出浆开关的同时,系统通过数据采集卡对浓度计进行约为10min 的抽样, 抽样间隔为1S;系统根据采样数据计算出加水量后,自动启动加水开关,并通过数据采集卡对流量计抽样计算加水量。当加水量满足时,系统自动停止加水开关。在加水过程进行时,进浆过程继续进行,直到矿浆溶液高度达到液位计高度时,系统根据传感器信号停止进浆。
出料控制过程:进浆过程结束后,系统根据生产需要启动搅拌电机,搅拌矿浆30min(可以设定),搅拌完成后计算出矿浆浓度等参数;当用户输入班产体积H每日产量I时,系统计算剩余矿浆压力,同时启动出料开关和软管泵,开始出料过程;出料中,系统实时检测压力计抽样值,当抽样值达到计算值预定精度范围时,停止出料开关和软管泵,出料过程结束。
根据上述控制过程,一次控制的主程序框图如图3 所示。
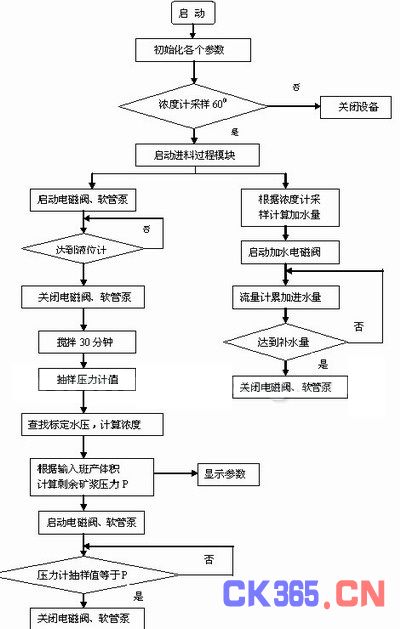
图3 主程序控制流程图
3 系统运行结果及其分析
系统运行时各个功能模块界面可以相互转换,图4 显示的是系统控制出浆过程时的界面。从图4 可看出,系统很好地反应了现场设备状态,实时显示了系统控制参数值及其曲线,对设定的参数值进行报警,很好的完成了生产设计的要求。
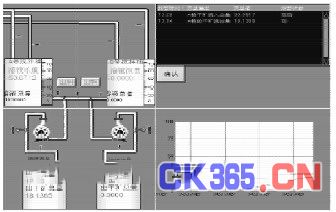
图4 部分系统运行图
系统总体运行结果良好,很好地满足了控制要求,达到了最初的设计目的。为保证系统的良好运行,在系统中除了对各控制量自动控制外,还设置了人工手动控制。在手动控制过程中,软件系统只负责监测。