一,引言
目前,变频器调速控制系统已广泛应用于汽车、机械、冶金、化工等各个行业。作为变频调速系统中的控制核心部分的变频控制器,最初是以单台形式工作的,可以通过变频器的控制面板或端子进行运行参数的设置,启动或停止变频器运行,读取各种变频器运行数据等等。而目前各种大中型自动化生产线则要求由多台和多种变频器组成的同步控制系统、比例控制系统、闭环控制系统等复杂的控制,并且要相互协调,形成连续生产线的调速控制系统。
本文取自我公司在某焊接车间的一个实例。叉式移载升降机在汽车焊接车间的应用目的是将车身焊接线上的白车身转移到空中滑撬上,通过滑撬机运系统送白车身进入B.I.W.线。叉式移载升降机在这个过程中需要与两个不同的系统交接,控制比较复杂,同时运用了同步和比例控制,并需要三个系统相互协调,满足工艺要求,提高产能和产品质量。该例采用PLC通过DeviceNet现场总线对SEW Movimot变频器、A-B PowerFlex700VC变频器进行控制,并有效的运用Versaview CE700 HMI对现场设备实时监控操作,实现了多机分布传动和联动机制的PLC集中监控和控制系统,着重介绍了本系统的硬件构成和组建过程及A-B PowerFlex700VC系列变频器实时在线通讯的实现。
二,工艺要求和系统工作原理
焊接车间白车身生产线上的叉式移载升降机控制系统主要由四台电机驱动。要求在与焊接线和空中滑撬线交接时能以不同的匹配速度,启动停止要求相对同步才能保证并提高生产,在生产过程中对设备的位置精度控制要求较高,误差精度高,故采用闭环控制系统来实现。
此过程工艺精度要求比较高,安全性能要求高,因此对电气控制精确度和安全性提出了较高的要求。具体工艺流程下图所示:
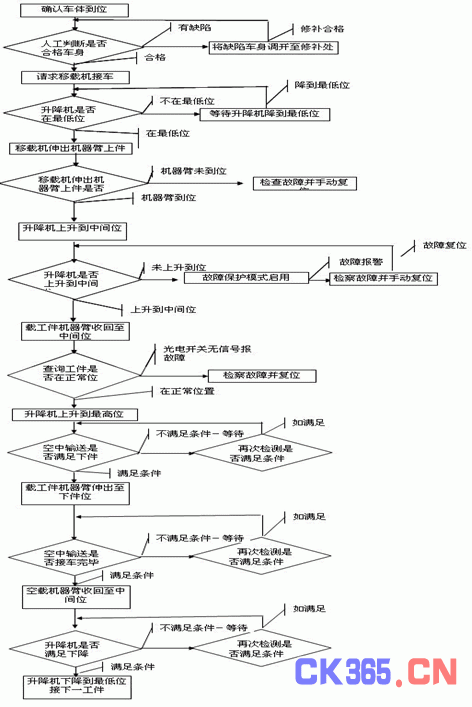
三,自动控制系统构成
根据设备工艺的技术要求我们设计了专门的全新控制系统,整个控制系统主要由以下几部分组成。
1.集成到Logix平台的变频器,通过给SEW Movimot变频器增加DeviceNet通讯适配器和给A-B PowerFlex700VC变频器添加20-COMM-D通讯适配器,进行网络控制;
2.运用AB PLC 的1756-DNB模块作为DeviceNet扫描器模块,通过网络对变频器进行控制;
3.通过PC HMI Versaview CE700来监控和操作,可以直观的显示各种参数和故障报警。便于维护和操作,系统的可靠性强,抗干扰能力突出,网络结构简洁。系统结构如图所示:
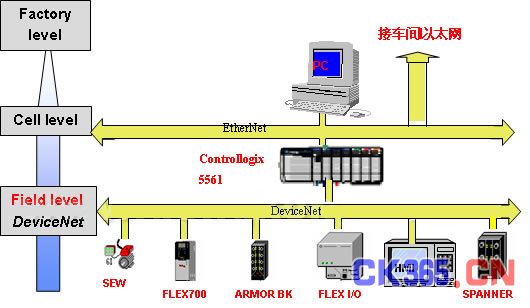
电气系统硬件结构于上图所示,主要由下列组件构成:
1)PC HMI(Versaview CE700 HMI)为整个系统的操作设置显示单元。在HMI上可以通过不同画面将PLC内部数据、输入(I)输出(O)状态、各个动作过程,以及全机故障查询、工艺参数等一一显示出来,实时监控全机的工作状态,除了显示功能外,还可以根据现场的情况,通过HMI设置和修改PLC内部的一些需要用户设定的参数。人机界面上直接观察到变频器的工作状态,对变频器进行监控。
2)AB Controllogix5561为PLC基本单元,执行系统及用户软件,是整个现场(Cell level)设备层的核心。
3)1756-DNB 是AB Controllogix5561平台与现场设备的DeviceNet通讯适配器,该模块的主要作用是PLC通讯系统中作为主站发给各个现场变频器信息,并接收和发送现场输入输出信号。我们将其作为DeviceNet通讯主站使用,完成变频器和现场设备各种数据的传送,参数监控及故障报警等。
4)SEW Movimot变频器自带DeviceNet接口单元和添加了20-COMM-D接口卡的 A-B PowerFlex700VC变频器符合DeviceNet通讯规范,用于PLC与现场多台变频器的联网,通过该单元能够在网络上实现变频调速器的运行控制(如启动、停止、运行频率设定)、参数设定和状态监控等功能,是变频器的网络接口,在工业现场,DeviceNet是应用广泛、运行稳定、技术成熟的一种通信。
5)A-B PowerFlex700VC变频器带有编码器PG闭环反馈,能有效的防止因负载的变化而引起的电机转速的变化,电机变频调速采用了编码器PG闭环反馈。该系统稳定特性较强,随负载变化而引起的变化小外界干扰对系统速度基本没有影响。保证了设备交接的吻合、位置控制的精确。
6)ODVA开放式标准的通讯网络,整个网络架构分为两个层级,上层为开放的以太网通讯Ethernet/IP,主要用于人机界面和PLC之间的通信;另一层为现场设备级的 DeviceNet网络,主要用于小范围(500米以内)的现场设备级控制,包括,IO、变频器等。由于Ethernet/IP与DeviceNet网络均采用统一的数据包格式,因此在这两者之间的数据通信无需在CPU内进行任何网络编程,完全实现了数据的无缝路由。
7)整个系统处于公司级上位机监控和操作下,能将实时数据反馈至公司主服务器,例如:产量、合格率、设备使用率等等情况,车间生产情况更加透明化,形成数字透明工厂的雏形。
四,A-B PowerFlex700VC矢量变频器与PLC的通讯原理及协议
变频器与PLC通讯是双向进行的,因此收发双方同时都具备收发设备,双方同用一个传输媒介,传输系统和交换系统共同组成一个完整的通讯系统,并由此构成复杂的通信网络。本系统基本上包含了通信方面的基本技术:编码技术、传输技术。PowerFlex700VC矢量变频器采用五线制的DeviceNet总线协议作为现场监控和操作协议。它以主从式方式构成工业监控网,在网络里有一个主站1756-DNB,1~63个从站,各站点由唯一的标识码识别。这样AB PLC和HMI,及上位机系统便能通过DeviceNet通信线,对网络上的所有设备进行控制操作。PowerFlex700VC通信方式为 DeviceNet,波特率最高可达500Kbps,本系统采用125Kbps;数据格式为4ByteIN、4ByteOUT。
变频器接收控制的通信协议如下:
逻辑命令字(Logic Command Word)
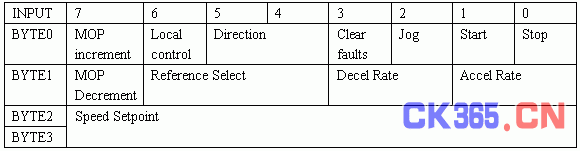
逻辑状态字(Logic Status Word)
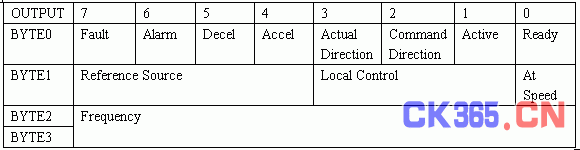
由通讯可以控制变频器的起/停、故障检测、故障复位、速度和转向控制,由PLC通过DeviceNet总线完成。
五,控制系统中变频器与PLC通讯控制软件设计
由于系统生产工艺要求精确度高,安全性能要求高,因此PLC与变频器之间的通讯的实时性和设备的响应时间是重点。要实现对变频器的实时通讯控制,要求PLC进行通讯编程,通过程序实现PLC与变频器信息交换的控制。
1,由于AB Controllogix5561平台功能强大,通过DeviceNet总线协议能够实时的监控各个设备所处的状态,能及时的检测出各个设备的通讯故障,系统中的PowerFlex700VC和SEW变频器都有强大的故障保护性能,当设备发生故障时,变频器开启自动保护,并同时发出故障报表,并将该设备进入故障安全状态,直至维修人员将故障排除并复位。
2,PowerFlex700VC的马达控制参数部分设定如下:
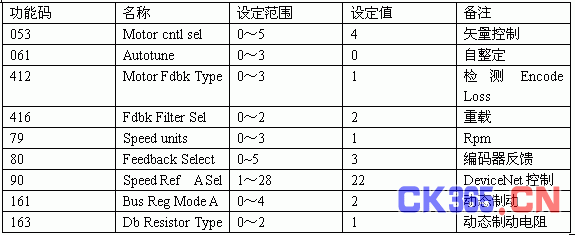
以上参数是部分修改的实际值,其余参数调整是按厂家出厂值或电机铭牌值进行设定,注意采用闭环编码器时,编码器的分辨率和转向。
六,Versaview CE700 HMI画面设计
在 PC级人机界面中,根据控制需要设计控制画面,包括主选择画面、模式画面、叉式移载升降机循环时间画面、DeviceNet总线监控画面、设备监控操作画面、设备交接连锁画面、整体区域监控画面、帮助画面、故障报警画面和密码保护等。故障显示使用具体故障名称和故障时间地点,让操作者很方便的知道故障原因和部位,极大的降低了维修时间,节约了运行成本。监控操作画面举例如图所示:
1,主选择画面:
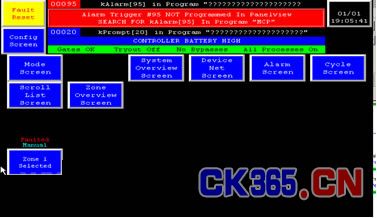
2,主操作画面:
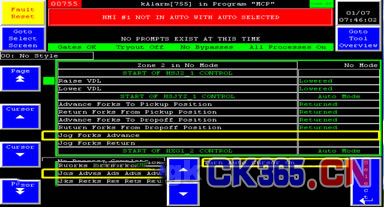
3,设备监控画面:
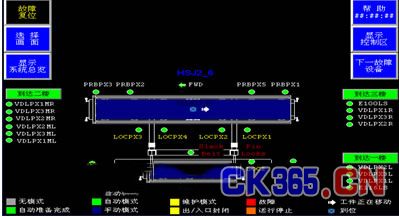
七,实际应用效果
经过汽车焊接车间实际应用,A-B PowerFlex700VC矢量变频器加编码器闭环组成的自动控制系统,在汽车工厂采用DeviceNet开放式总线控制是一种理想的控制方式,非常适合大规模使用,它有很多值得借鉴的优点