一 概要
武钢燃气厂煤气第二混合站把炼铁厂生产的高炉煤气(以下简称高煤)和焦化厂生产的焦炉煤气(以下简称焦煤)按用户对热值的要求进行配比混和,然后向大型、轧板、高线等十几个用户提供压力、热值稳定的混合煤气。由于以前生产控制工艺本身存在缺陷,自混合站投运以来的十几年间均无法实现系统的全自动跟踪调节。在武钢“二吹二”的系统工程中,由武钢计控公司自主设计、设备选型、编程调试以及施工的“二混”项目,选用了冶金自动化研究院提供的美国Smar公司生产的基金会现场总线控制系统System302,同时采用目前国内所独有的两阀控制方案实现了系统的自动调节与控制。自投运以来系统运行稳定、调节品质较好。
二 系统控制方案的由来
图1是改造前,二混的生产工艺流程以及控制原理示意图。控制的目标是实现混压稳定,并能按用户对热值的要求通过焦煤和高煤的流量配比,实现热值自动控制。
以前的控制系统采用四阀控制方案。前两道阀门采用单回路压力调节来调整混合前的压力稳定。后道高煤阀也采用单回路压力调节以保证混合压力稳定,后道焦煤阀对焦煤和高煤的流量进行配比调节,实现对混合煤气热值的控制。生产实践中,焦煤的混合前压力为20~24kPa,高煤为21~25kPa,而用户要求的混合压力则为20±1kPa。但是由于管道中节流件、取压部件、大小头、管道以及阀门翻板的压力损失,使得管道中的这些沿程阻力和局部阻力之和较大,后两道阀门的阀前后可调压差不足1kPa。而目前国内最好的蝶阀能满足的可调比约为10:1,即使国外最好的蝶阀可调比可达到30:1,但采用四阀方案很难满足阀门对可调比的要求,在实际生产过程中,四阀控制方案也根本无法实现。有鉴于此,为降低管道压力损失,从而实现自动控制,本计控公司大胆采用国内尚无任何成功经验的两阀控制方案,取消前两道压力调节阀,并选用环型节流孔板来降低节流件上的压力损失,以提高阀门前后的压差来实现系统的自动控制方案。考虑到整个系统的安全以及FF现场总线在过程控制领域的优势,我们选用美国Smar公司的现场总线控制系统——System302。
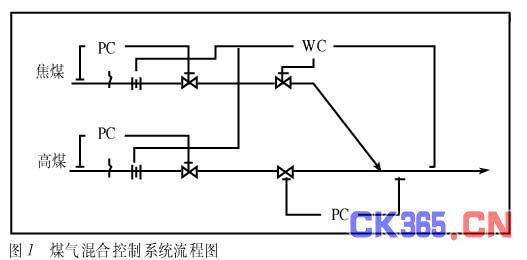
三 控制系统硬件配置
本系统由单操作站作为HMI(人机接口),PCI卡作为操作站SCADA的接口。考虑到煤气混合站的安全要求而选用了总线安全栅SB-302,同时为了便于总线的数字信号与普通模拟信号间的转换和采集,采用Smar公司的带有万能现场总线接口模块的PLC 产品LC-700。总线采用的是适合热工过程自动化的H1低速总线,网络拓扑采用的是较为安全可靠的树型结构,整个控制系统硬件配置如图2所示。
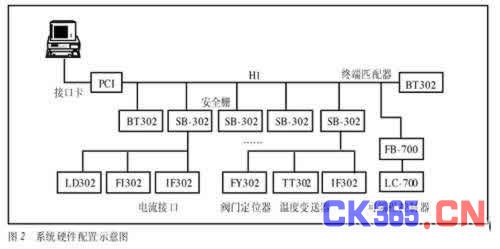
每个总线可挂4台安全栅,每个安全栅后可挂3~4台变送器或阀门定位器,较DCS系统节省70%电缆,这对于像控制室距现场远达2km的工程(如我公司四混、三混)确有明显节省材料和施工费用的效益。
控制和计算功能分布在变送器和阀门定位器中,系统硬件简洁,没有仪表盘柜,少量硬件仅布置在操作台下,节省了控制室面积。由于是总线系统,布线极少且简单。
四 系统控制策略
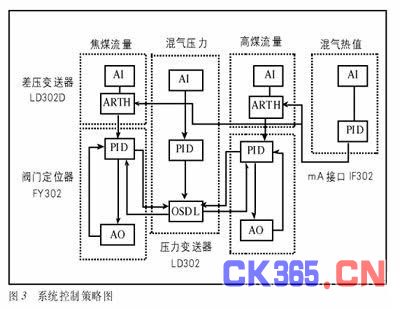
系统控制策略如图3所示,图中虚线框是物理的现场总线设备,实线框是下装的软件功能块,设备间联线表示通过现场总线的通信。这是一个压力、流量串级调节和热值配比调节系统,而且两者间要实现零耦合,互不影响。这种控制完全分散的模式被称为“鸡脑神经”网络,是一种高可靠的自控模式。目前国内像武钢这样的工况,每小时用量达5~10万立方米的大型混合站,尚无成功的两阀控制方案,宝钢采用的是四阀分层调节。我们的控制方案关键在于首先通过热值配比在计算块中运算来避免流量的大幅波动,其次是采用了动态交叉限幅输出选择模块,通过它来减小压力和流量调节中带来的相互间大的干扰,避免系统出现振荡。控制策略是实现系统自动控制的基础,同时它要保证把调节输出信号间的干扰减小到最小,然后是通过参数的整定来避免调节信号间的耦合,使自动调节达到较好的品质。
五 工程调试中的问题和解决方法
1. 系统的互可操作
工程中实现了FF现场总线下System302与Fisher阀门定位器的互可操作。由于工程设计者选用了支持基金会总线协议的Fisher数字阀门定位器,这样就存在一个System302与Fisher阀门定位器之间互可操作的问题。
互可操作是现场总线技术的重要特点之一。它包括两方面的的含义:(1)设备的可互换性,指对于具有同一功能但来自不同厂家的设备可以实现互换;(2)设备的可互操作性,指不同厂家的设备可以实现互相通信,正确理解和交换数据的含义,完成系统所要求的功能。
FF 现场总线实现互可操作性有两大关键技术:功能块和设备描述(DD)。
完成互可操作的具体步骤如下:
(1)安装DD(设备描述文件)
由现场总线基金会定义的设备描述的路径结构如下:
...xxxxxyyyrrddvv.eee
其中:...是主机系统所执行的访问DD结构的路径;
xxxxx是由现场总线基金会所确定的制造商识别号;
yyy是制造商定义的设备型号;
rr是制造商定义的设备版本号;
dd是由制造商确定的其设备所用设备描述(DD)的版本号;
vv是由制造商确定的其设备所用设备描述(DD)或通用文件(CFF)版本号;
eee是文件的的扩展名。
把Fisher的DD 拷贝到系统路径下即可。
(2)完成系统配置
在070101.cff中加入:
MaximumNumber of linkage objects=50
MaximumNumber of linkage objects=2
在Standard.ini中加入:
005100 fisher
[005100 device by code ]:fisher device types
5400=DVC.5000f
005100 5400 07 01 80020310=RES
005100 5400 07 01 80020530=TRD
005100 5400 07 01 800201F0=AO
005100 5400 07 01 800202B0=PID
做完以上的工作,经过对功能块间的数值传递测试和功能测试,就基本完成了Fisher阀门与Smar控制系统的互可操作。
2. 提高了系统的数据响应时间
系统共有设备16台,挂在两条总线上。调试中发现,理论上一条总线最多可挂16台设备,但在实际中,由于策略复杂或总线上链接通信多,都可能导致系统数据响应较慢的问题。系统组态软件SYSCON可显示总线扫描的宏周期(Macro-cycle),即所有功能块和链接通信执行一次的时间,以500ms以下为宜。实际中使用了两条总线,把相互关联的设备置于同一条总线下,其中一条总线挂12台设备,另一条挂5台设备。若干个宏周期构成一个监控周期即所有和操作站交换的信息执行一次,需要3~5s,完全满足了生产的要求。(经试验,如16台设备同挂在一条总线下,由于控制策略复杂,在操作站修改一个现场数据大约长达30s才能完成,显然太慢。)
3. 系统参数的整定
系统投运开始阶段,出现了阀门无法稳定,有大约10%的来回波动,自动投运时系统稳定性差,准确性不好的问题。经分析发现造成问题的原因为:(1)阀门本身的PID与系统PID作用迭加后造成了阀门的振荡;(2)流量的滤波时间较短,是系统的稳定性差的一个原因;(3)流量和压力之间有一定的耦合使得系统振荡;(4)用户不稳定,系统的扰动大;(5)加压机的出口压力变化较大,即阀前压力波动大。
针对这些问题,从系统的角度综合考虑稳定性、准确性、快速性来整定系统的参数,做了以下的工作:(1)把阀门本身的PID整定至最佳,力求稳定不振荡,适当放弃快速性;(2)尽可能加长流量的滤波时间,以求得系统的稳定;(3)压力调节回路和流量配比调节回路的PID参数整定应考虑被调对象的流程时间,通过整定时间常数来实现调节作用间的零耦合。
通过这样一番整定,系统取得了非常好的效果。混压稳定在设定值的±0.3kPa,流量配比误差为±500m3。
六 基金会现场总线技术的优越性
现场总线技术促使现场设备向数字化、智能化、网络化发展,数字化和开放性是各种现场总线的基本特点。而现场设备的智能化,现场设备丰富的信息则是FF现场总线技术对比DCS/PLC的远程I/O及其他类型现场总线的突出优势。而这些优点又可通过“功能块参数”来理解。FF现场总线的几十个功能块可分为3类(如表所示)。

每个功能块有几十个参数,所谓丰富的现场设备信息均在其中。按用途又可把功能块参数分成系统用,过程变量、标定调整用,诊断报警、管理记录用,于是在DCS概念的操作站和工程师站的原有功能上又增加了对现场设备管理的功能。
基金会现场总线过程变量参数由“数值”和“状态”两部分构成,其状态表达数值是:“好”、“坏”、“不确定”和“未使用”;如果是坏,则系统不予采用该数值并采取措施,如自动转手动、报警等。而且每种状态还细分为若干子状态,如传感器故障、超越量程、通信错误、组态错误等。这事实上是将系统置于连续的自诊断状态下,将减少停车检查时间和维护量,提高系统可靠性。
又如阀门定位器的功能块参数中包括了实际阀位,在操作站上很容易同时看到设定和实际阀位,而在DCS系统则要增加一根电缆和一个I/O点才行。
阀门定位器的功能块参数中还包括了阀位小闭环的调节参数(P,I),这样在操作站上就可以将阀门本身品质调好。
阀门定位器的功能块参数中还包括特性选择、自动标定等,这给系统调试和运行带来很大方便。